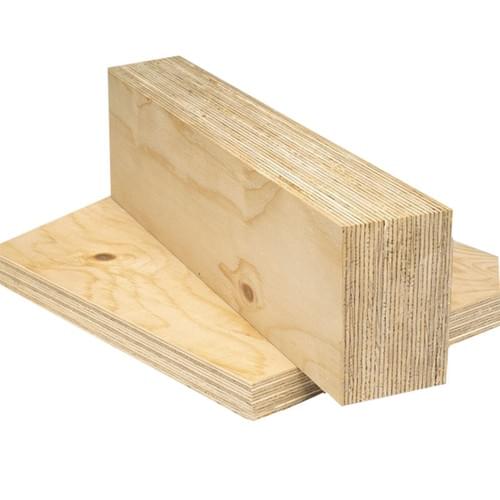
Structural LVL/Construction LVL/LVL Beam
Product name | Structural LVL/Construction LVL/LVL BeamVL Laminated Veneer Lumber |
Materials | Pines, Encalyptus, Combi, etc. |
Size | Width X Thickness: 90X35, 90X45, 140X45, 150X45, 190X45, 200X45, 240X45, 300X45, 360X45, 400X45, 90X63, 140X63, 150X63, 190X63, 200X63, 240X63, 300X63, 360X63, 400X63, 450X63, 95X65mm etc. Length up to 12000mm. |
Color | Natural or customized |
Density | Poplar, Hardwood, Combi , Birch, Eucalyptus |
Formaldehyde emission | E0,E1 |
Glue | Phenolic A-Bond |
Usage | Construction |
MOQ | 1X20GP for 16CBM |
Leading time | 15 - 30 Days |

LVL PRODUCTION PROCESS:
STEP1: Cut the log to size.
STEP 2: Peeling the Log to the veneer.
STEP 3: Drying the Veneer.
STEP 4: Grading the Veneer. A, B, C.
STEP 5: Gluing the veneer.
STEP 6: Laying the veneer.
STEP 7: Hot pressure.
STEP 8: Sanding the core.
STEP 9: Cutting to size.
STEP 10: Packaging.
Advantage of LVL
LVL product has many advantages over sawn milled lumber:
- LVL can be made from various veneer materials poplar, pine, acacia, eucalyptus, rubber, …
- LVL can control the specification: LVL can be produced in almost Thickness, Width, Length, Moisture Content, Uniform. The length of the LVL is not dependent on the log size, due to the manufacturing technique
- LVL is a high strength, but very lighter than sawn timber. Lower price.
- Using wood resources efficiently.
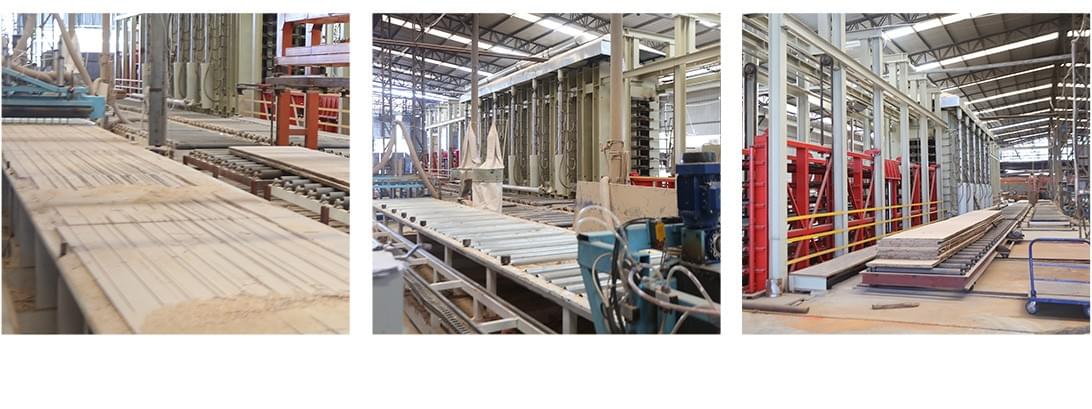

2) Outer packing: Pallets are covered with 2mm package plywood or carton and then steel tapes for strengthening.
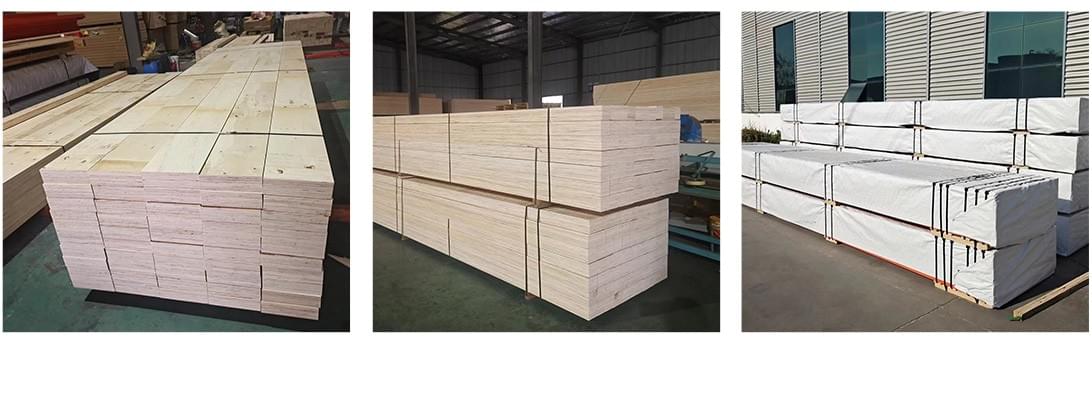

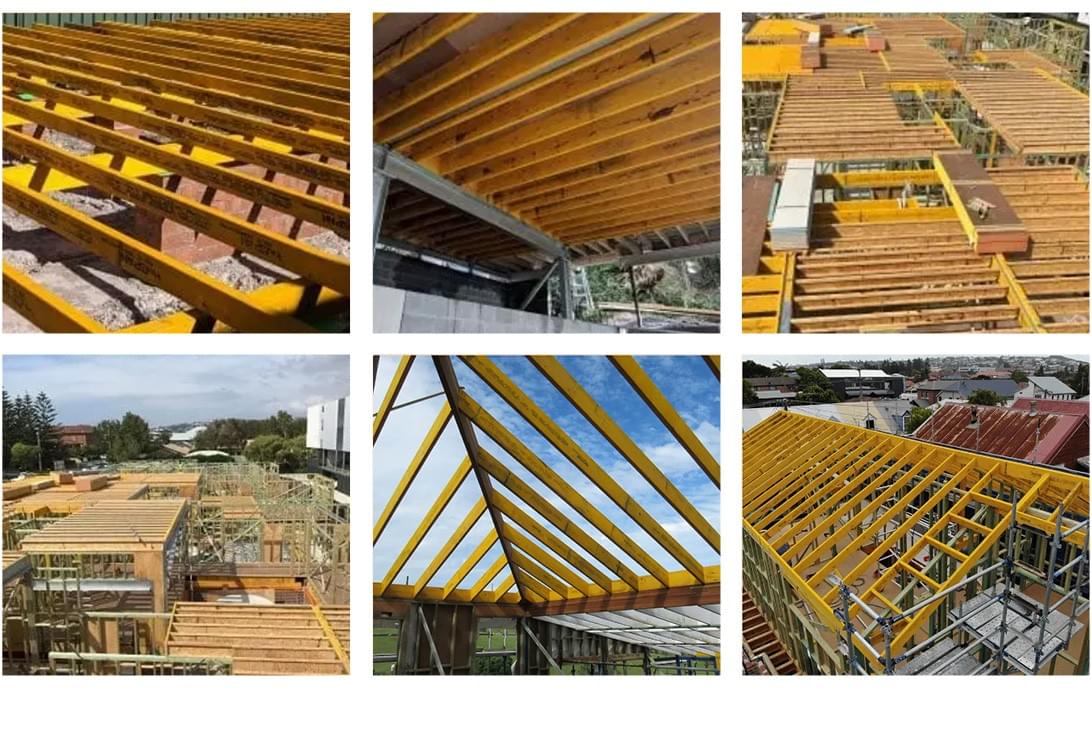